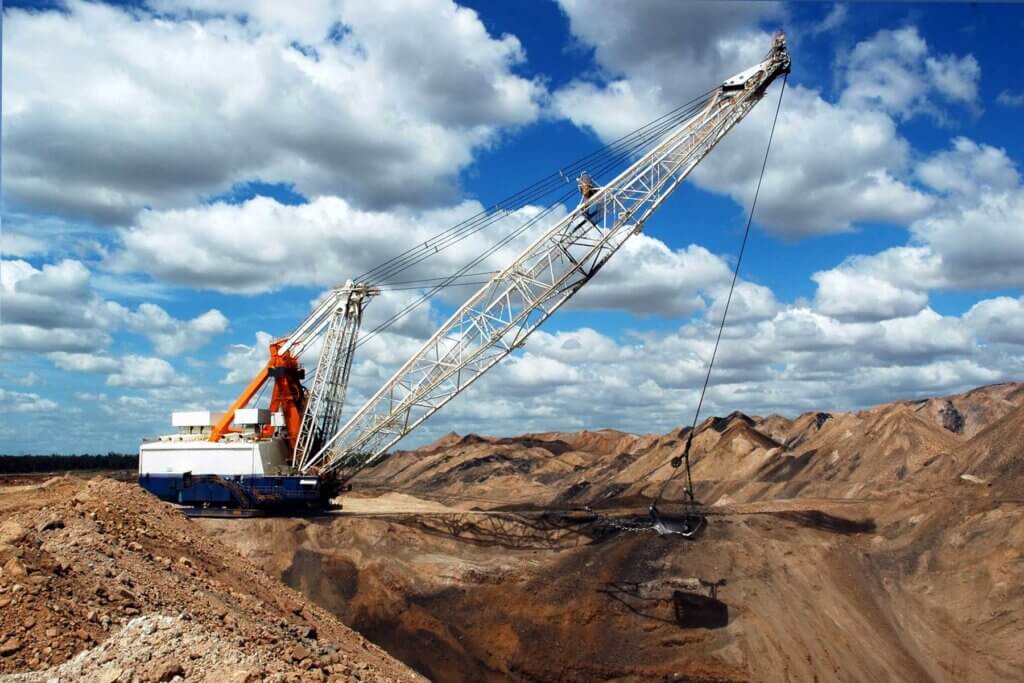
Project Overview
FLANDERS AC & DC dragline upgrades increase productivity worldwide
Draglines are the workhorses of surface mining operations, and reliable and efficient operation is critical to success. However, the inherent disadvantages of utilizing DC motors and MG sets can significantly impact productivity and return on investment (ROI).
Verified Results
Field-proven performance
Armstrong Coal’s dragline operators have been unanimous in their praise of the upgraded dragline, citing one-touch start-up (no need to start MG sets in the house); the machine’s torque and power; the high degree of coordination between all motions; and smoothness of operation. Armstrong reports that the AC dragline has been working flawlessly with availability in the upper 90% range since commissioning.
Given the energy efficiencies, precise control, and increased productivity available through AC dragline operation, mine operators who upgrade from DC to AC draglines stand to realize a quick ROI and ongoing improvements in productivity and safety, decreased cost-per-ton, and decreased total cost of ownership.
The Challenge
Given the extremely demanding conditions under which draglines operate, it was recognized from the onset of the project that taking a “built-for-purpose” approach to the upgrade would ensure the highest quality and increase the mining company’s ROI while decreasing its total cost of ownership (TCO).
FLANDERS designed the AC upgrade to conform to the existing physical envelope and footprint of the DC machine. The built-for-purpose AC motors were designed as drop-in replacements using the existing couplings and brake assemblies. This approach saved considerable time during the commissioning process. In addition, FLANDERS’ in-house power generation capabilities (both 60Hz and 50Hz) allowed for full load testing of the AC components and setting the operating parameters prior to delivery — another significant time saver.
The Solution
In 2010, when FLANDERS’ electrical, mechanical and systems engineers had completed 75 percent of their first AC dragline upgrade, Armstrong Coal shipped the DC rotating equipment and electronics from a dragline to FLANDERS for evaluation and a repair quote. The DC motors were in poor condition and the MG sets needed replacement. FLANDERS proposed upgrading the machine’s operation to AC power. The team designed, built, and delivered a fully operational AC dragline upgrade that has exceeded the customer’s expectations.
The team incorporated select power components with high thermal life cycle capability; ease of maintenance and repair by using easy-to-replace common power modules and detailed diagnostics as well as improved productivity and machine availability through water-cooled semiconductors to remove the heat from the house and allow cabinets to remain closed and filter-free. The control power was separated from the power section, reducing the risk of arc flash exposure, and achieving Level 0 arc flash within the control cabinet.
The purpose-designed drive systems provide maximum machine availability and are designed for long-life operation—up to 175,000 hours/10 million load cycles.
At Armstrong’s request, FLANDERS incorporated motor control centers (MCCs), an operator chair, and a temperature-loop VFD-controlled house blower. Several additional options can be added to suit the mine operator’s specific needs, including:
- Opportunity for Advanced Control
- Open system configuration allows for the interface of smart instruments, network devices, and advanced machine monitoring.
- Control expandability and enhancements
- Communication between drive processors
- High-speed data transfer for control
- Coordinated operation to dampen or prevent electro-mechanical interaction of motors and gears
Given the energy efficiencies, precise control, and increased productivity available through AC dragline operation, mine operators who upgrade from DC to AC draglines stand to realize a quick ROI and ongoing improvements in productivity and safety, decreased cost-per-ton, and decreased total cost of ownership. — Mike Casson, Business Development Director of Mining and Mills
Outcomes
AC technology in mining applications has been proven over the course of several years. The improvements realized by Armstrong Coal Co. included performance, efficiency, and safety.
- Performance: Precision of operator control is crucial for higher productivity. Today’s modern AC drives incorporate insulated gate bipolar transistors (IGBTs) in both the inverter section and the AFE, allowing for precise regulation of the power factor and producing speed control that exceeds that obtainable by DC-powered equipment. AC drives and coordinated AC motors provide enhanced performance capabilities that can significantly reduce cycle times.
- Efficiency: Energy costs strongly impact mining operations’ cost-per-ton. AC drives produce overall efficiencies approximately 12 percent higher than DC-powered systems and has no high inrush surge at start-up. AC drives consume virtually no power while idling in non-digging situations.
- Safety: Even a minor failure of high-voltage equipment can produce serious injuries. AC drive technology separates the control power from the power section, reducing arc flash exposure and achieving Level 0 within the control cabinet. Eliminating exposed commutators removes the risk of shrapnel from catastrophic failure and increases operator and maintenance personnel safety. Liquid cooling of AC drives decreases noise and heat levels in the house. Finally, the down-sized trailing cable — made possible by the lack of inrush at start-up — reduces the risk of physical injuries due to cable handling.
AC technology is the future of heavy industry. Click here to learn more about FLANDERS AC technology and how it applies to a variety of machines and industries.