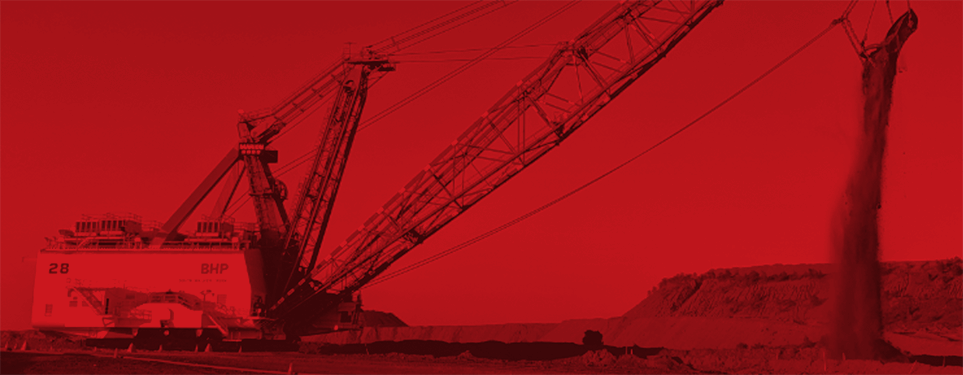
PROJECT OVERVIEW: The power of AC
In an age when efficient, energy-saving solutions are driving decisions across the mining industry, the future of AC draglines is bright. Based on verified data, FLANDERS’ AC retrofit is the definitive way forward for cleaner, safer, and more effective dragline work.
VERIFIED RESULTS
The Challenge
In 2018, the DRE28 DC 8050 dragline’s DC rotating equipment and DC Control system had reached the end of their operating service life. Ongoing maintenance and an increased risk of machine downtime prompted project managers to solicit solutions from their partners. FLANDERS came forward with an AC retrofit solution, providing the safety advantages of a closed system, the same service life expectancy, and reduced maintenance costs compared to the outdated DC systems. In July 2019, the boom was lowered on DRE28 DC 8050 and the on-site retrofit began.
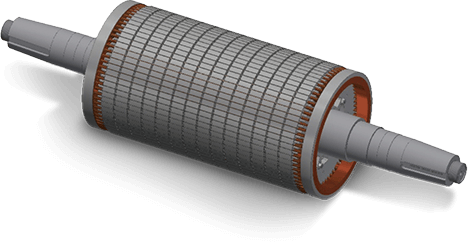
The Solution
AC systems are designed with safety built in. Hardware compatibility and simplified, safer operating mechanisms, and scalability are benchmarks of FLANDERS’ AC system design.
Drive Cabinet
- Replaces DC motor-generator (MG) sets.
- Water-cooled semiconductors remove heat so the cabinets keep parts protected from debris.
- Reduction in noise, dust, heat, and rotating parts, and reduced or zero exposure of employees and maintenance technicians to these same safety hazards associated with DC systems.
- Eliminates the need for on-site machining to blow out dust, balance parts, clean brushes, and other regular maintenance DC systems require.
AC Hoist/Drag Motors
- Designed to fit in the same size box as the DC motor allowing for easy drop-in installation.
- No modification necessary.
Arc Flash Safety System
- Category zero arc flash rating, eliminating the need for isolation or specialists for access.
Ground fault detection
- Eliminates the risk of electric shock, providing a system shut down override at the sign of a catastrophic event.
Optimization
- DC commutators are limited in output
- AC systems can continue to be optimized on site to achieve better results
- Full potential of AC systems yet to be unlocked
The overwhelming response from our client was related to the safe and easy operation of the AC system. Operators were vocal with management about the improved work conditions. — Owen Uebel, Strategic Business Development Manager
Outcomes
In two years of operations, the mine has reported significant returns from the AC dragline retrofit. A twelve-month comparison study showed the AC 8050 moved an additional 2 million BCM compared to the DC 8050.1 A return on investment was achieved within 18 months of the AC 8050 going online, making it the lowest-cost pre-strip solution on the market.
In July 2021, a system optimization increased the system’s peak power, resulting in a 4.5 second reduction in cycle time with no additional structural or mechanical stress on the machine.2
- 4.5 second reduction in cycle time
- 18 months to achieve ROI · $450k savings per year
- 60% decrease in maintenance costs
1Based on MineWare daily reports from January 1, 2020 to December 31, 2020.
2Based on MineWare daily reports from January 1, 2020 to December 31, 2021.
For a more in-depth look at this case study, view and download the full white paper below.
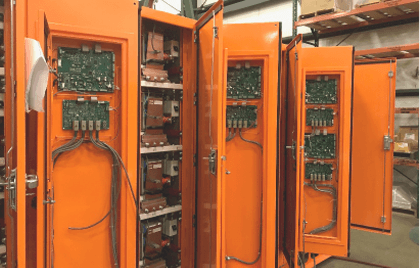